The
powder coating curing oven plays a pivotal role in attaining a long - lasting and top - notch powder - coated finish. This crucial equipment is the linchpin in the powder coating process, as it transforms a simple layer of powder into a resilient and aesthetically pleasing protective covering. There are two primary types, each catering to distinct needs within the manufacturing and DIY sectors.
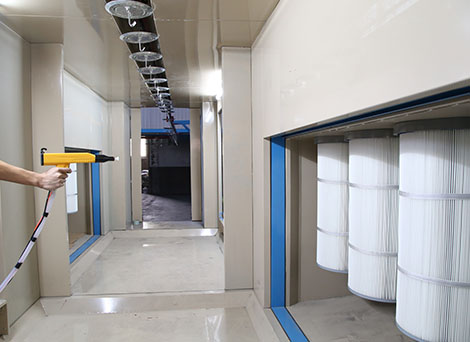
The small - scale benchtop curing oven, with a starting price of approximately $500, is ideal for hobbyists and small DIY workshops. Measuring around [X] inches in length, [Y] inches in width, and [Z] inches in height, it is compact in size, easily fitting onto a standard workbench without taking up much space. It is equipped with basic temperature - control functions, allowing users to set the temperature within a certain range, usually from [lowest temp] to [highest temp], which is more than sufficient for small - scale projects. This type of oven often comes with a simple digital or analog display, making it easy for beginners to operate.
The industrial - grade curing oven, starting at $5000, is engineered for large - scale production. It is designed to handle high - volume manufacturing demands. With a capacity to hold multiple large - sized workpieces simultaneously, it features precise temperature control that can maintain the set temperature within a very narrow tolerance, ensuring consistent quality across the production line. The high - volume capacity can be, for example, up to [XX] cubic feet, which is perfect for large - scale production facilities. It also incorporates energy - efficient heating elements, such as advanced infrared or ceramic heating elements, which not only save on energy costs but also heat up the oven more quickly and evenly.
These ovens operate by applying heat to fuse the powder coating onto the workpiece. The heat source, whether it's electric, gas - fired, or another type, gradually raises the temperature inside the oven. As the temperature rises, the powder coating on the workpiece melts and flows, eventually forming a smooth, uniform layer. They are built with insulated materials, such as high - density fiberglass or polyurethane foam, to retain heat and ensure uniform curing. This insulation not only improves the efficiency of the oven but also reduces heat loss to the surrounding environment, making it safer to operate. Suppliers typically provide installation guidance, which may include step - by - step instructions on how to set up the oven, connect the electrical or gas lines, and calibrate the temperature control system. They also offer operator training, covering aspects like proper loading and unloading of workpieces, how to set the correct curing parameters, and safety precautions. After - sales maintenance support usually includes regular check - ups, replacement of worn - out parts, and troubleshooting services.
In the jewelry - making industry, the benchtop oven can be utilized to cure powder - coated metal jewelry. Jewelers can carefully place their delicate pieces inside the oven, set the temperature according to the specific powder coating used, and let the oven work its magic. This results in a beautiful, durable finish that protects the metal from tarnishing and gives the jewelry a unique look. In automotive parts manufacturing, industrial - grade ovens are employed to cure coatings on engine components. These components, such as cylinder heads, pistons, and crankshafts, need a high - quality coating to withstand the harsh conditions inside an engine. The industrial - grade ovens ensure that the powder coating adheres firmly and evenly, providing long - term protection and performance.
A: Refer to the guidelines provided by the powder manufacturer. These guidelines usually come in the form of a technical data sheet that specifies the recommended curing temperature range for different types of powder coatings. Adjust the temperature control knob or digital settings accordingly. If it's a digital control panel, you may need to use the arrow keys or touch - screen interface to input the desired temperature.
A: Check the temperature rise rate. A too - rapid increase might lead to bubbles. For example, if the temperature rises too quickly, the solvent or air trapped within the powder coating may not have enough time to escape properly, causing bubbles to form. Additionally, ensure that the powder is dry before curing. Moisture in the powder can also cause bubbling during the curing process. You can store the powder in a dry, air - tight container and use a moisture - absorbing agent if necessary.
Q: Can I use the oven for different kinds of powder coatings?
A: Yes, but be sure to clean the oven thoroughly between different powder types to prevent contamination. This involves removing any remaining powder residue from the oven walls, shelves, and heating elements. You can use a soft brush, a vacuum cleaner with a suitable attachment, or a mild cleaning agent to ensure that no traces of the previous powder coating are left behind.
A: Clean it after every 5 - 10 uses. Remove any powder residue to prevent it from burning and influencing the curing process. When powder residue accumulates and burns, it can release harmful fumes and also create hot spots inside the oven, which can lead to uneven curing. Regular cleaning helps maintain the performance and longevity of the oven.
A: Take into account your production volume, budget, and the size of the workpieces. For small - scale projects, a benchtop oven suffices. It's cost - effective and easy to operate, and its small size is perfect for handling a limited number of small - sized workpieces. For large - scale industrial production, an industrial - grade oven is more appropriate. Its high - volume capacity, precise temperature control, and energy - efficient features make it suitable for meeting the demands of mass production. You should also consider future growth potential; if you anticipate an increase in production volume in the near future, it might be wise to invest in a slightly larger or more advanced oven from the start.
Disclaimer: Enhance your coating process with advanced electrostatic powder coating machines, precision powder coating spray guns, comprehensive powder coating systems, and efficient powder coating lines from Hangzhou Huaxiang Coating Equipment Co., Ltd. Designed for reliability and high-quality finishes, our solutions meet all your industrial powder coating machine needs. Contact us at sale3@cncolourspray.com